Memory Foam Mattress: A Guide to Understanding the Manufacturing Process
Are you in the market for a new mattress? If so, you may have come across memory foam mattresses. These types of mattresses have become increasingly popular in recent years due to their ability to provide a comfortable and supportive sleep surface. But have you ever wondered how these mattresses are made? In this article, we will delve into the top 10 manufacturing processes for memory foam mattresses.
1. What is Memory Foam?
Before we dive into the manufacturing process, let's first understand what memory foam is. Memory foam is a type of polyurethane foam that is known for its ability to conform to the shape of a person's body. It was first developed by NASA in the 1960s to provide cushioning for astronauts during space flight. Today, it is widely used in mattresses, pillows, and other bedding products.
2. The Benefits of Memory Foam Mattresses
Memory foam mattresses offer a range of benefits, including pressure relief, motion isolation, and durability. The foam's ability to conform to the body's shape helps alleviate pressure points, making it an excellent choice for those with back pain. Additionally, memory foam mattresses are known for their ability to isolate motion, making them an ideal choice for couples who don't want to be disturbed by their partner's movements. Lastly, memory foam mattresses are highly durable and can last up to 10 years with proper care.
3. The Manufacturing Process
The manufacturing process for memory foam mattresses involves several steps, including mixing, pouring, and curing the foam. Let's take a closer look at each of these steps.
4. Mixing the Foam
The first step in the manufacturing process is mixing the foam. The ingredients, which include polyol and isocyanate, are mixed together in a large vat. The amount of each ingredient used will determine the density and firmness of the foam. This mixture is then left to sit for a few minutes to allow for proper expansion.
5. Pouring the Foam
Once the foam has expanded, it is poured into a mold. The mold is typically in the shape of a mattress, and the foam is poured in layers to ensure even distribution. The foam is then left to cure for several hours.
6. Cooling and Cutting
After the foam has cured, it is removed from the mold and cooled. Once cooled, the foam is cut into the desired size and shape. This step is crucial as it ensures the foam is the correct size for the mattress and any additional layers or features.
7. Adding Additional Layers
In some cases, memory foam mattresses may have additional layers, such as a base layer for support or a cooling layer to regulate temperature. These layers are added during the manufacturing process and are carefully placed on top of the memory foam layer.
8. Sewing the Cover
After the foam layers are assembled, the cover is sewn onto the mattress. The cover is typically made from a stretchy, breathable material that allows for the foam to conform to the body's shape. This also helps with temperature regulation and moisture-wicking.
9. Quality Control and Testing
Before the mattress is packaged and shipped, it goes through a series of quality control and testing measures. These include checking the foam's density and firmness, ensuring the cover is properly sewn, and testing the overall comfort and support of the mattress.
The Benefits of Memory Foam Mattresses

Superior Comfort and Support
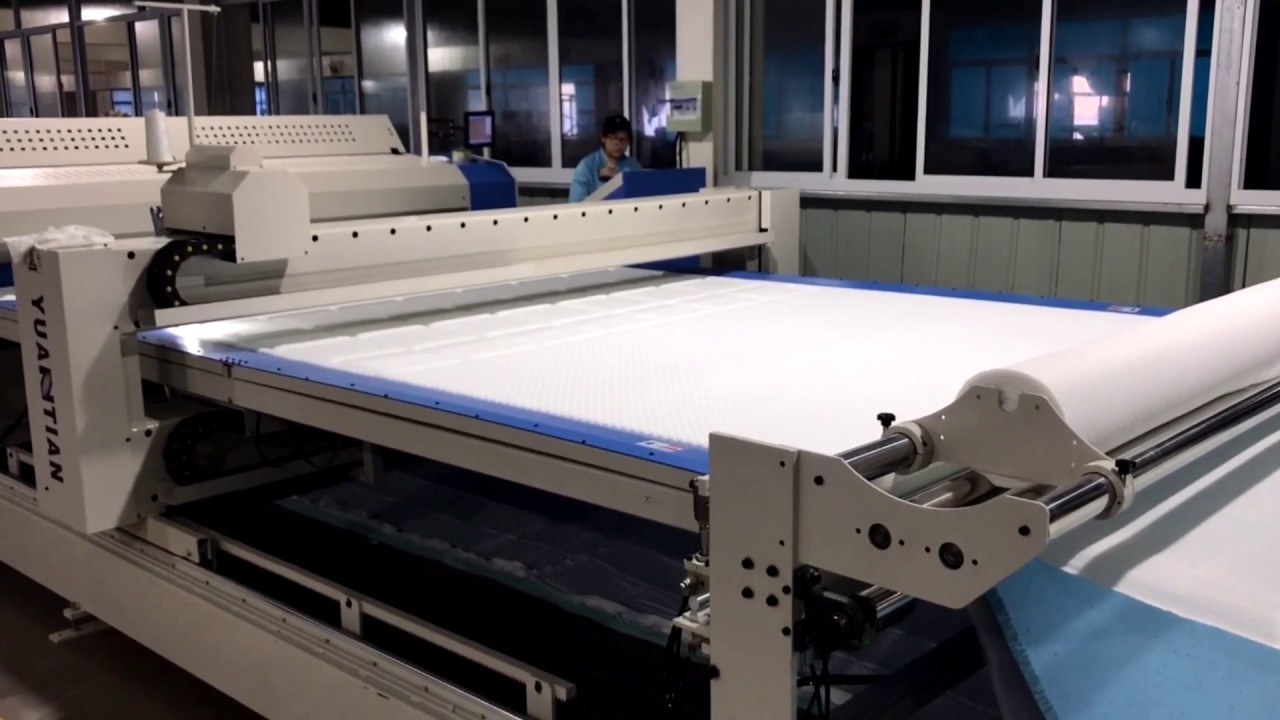
Improved Spinal Alignment

Reduced Motion Transfer

Durability and Longevity

Hypoallergenic and Dust Mite Resistant
